Multi-Tasking Turn-Mill Swiss Type Machine controller
High-Speed, High-Precision Serial Motion Control.
Extended Controller specifications
Our FULL option 220TB controller
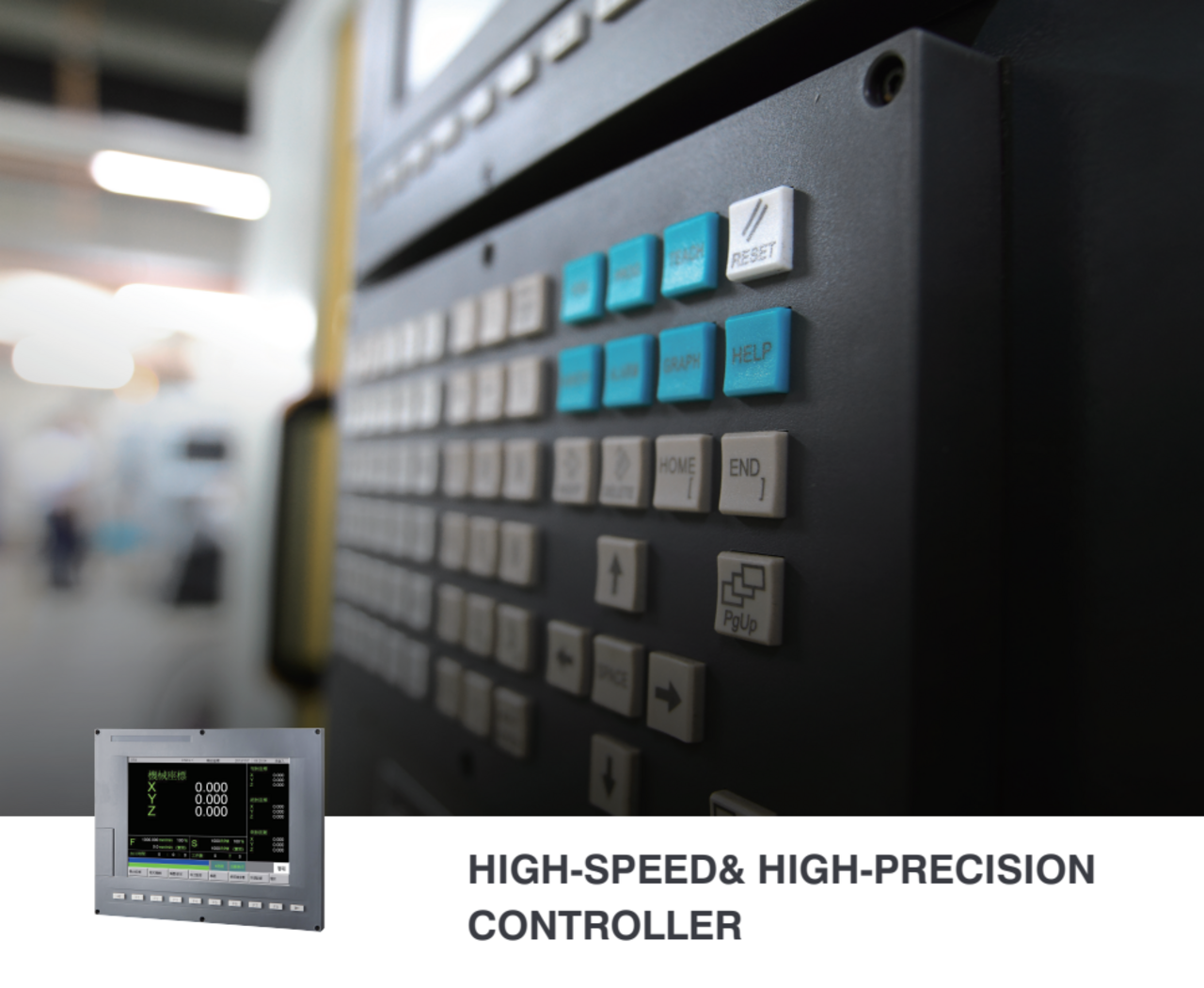
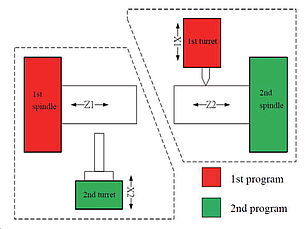
Axis Exchange Control
The tools of the first axis groups can be synchronously machined with the second spindle; and at the same time the first spindle occupies the second tool group from subspindle to machine. Reduce the number of machine tools, machine more flexibly, and improve machine efficiency.
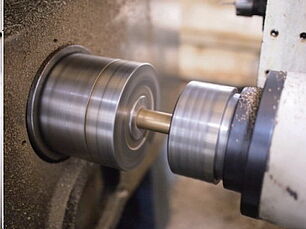
High-Speed Spindle Synchronization Function
Function of synchronizing the rotation speed and angle of two spindles
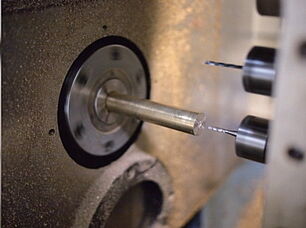
Twin Spindles Tapping
Significantly reduction of time for tapping.
None of the spindles does need to decelerate speed to zero, or even maintains the original speed, so any spindle and tool holder can execute tapping at different speed, which significantly reduces required time for tapping.
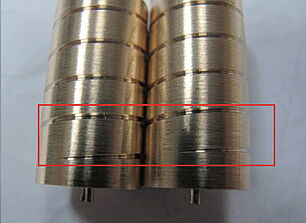
Extreme Speed Threading Mode
Improving tool retraction movement in threading cycle creates the beautiful thread; the high speed thread cutting mode can enhance threading efficiency
1000 Time Threading | General Threading | Extreme Speed Threading Mode | Time Saving |
G21Threading | 36789(Sec) | 29303(Sec) | About 20.3% |
G78Threading | 24685(Sec) | 18803(Sec) | About 23.8% |
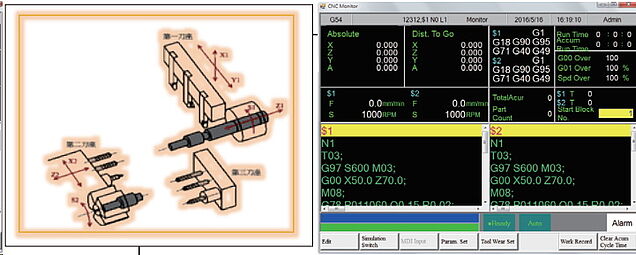
Dual-Paths Mill-Turn Solution
G-code list with extended functions standard in Robotturn
Our controller offers more than the Fanuc controller reference controller
Fanuc Ot G-Code List | |||
Fanuc | Robotturn | ||
G Code | Extra G-code | Function | |
G00 | Positioning (Rapid traverse) | ||
G01 | Linear interpolation (Cutting feed) | ||
G02 | Circular interpolation CW or helical interpolation CW | ||
G02.1 | Elliptical cutting (clockwise) (G02.1) | ||
G02.2 | Parabolic cutting (clockwise) (G02.2) | ||
G03 | Circular or/and helicalinterpolation CCW | ||
G04 | Dwell | ||
G07.1(G107) | Cylindrical interpolation | Cylindrical interpolation (G07.1) | |
G08 | Advanced preview control | ||
G10 | Programmable data input | ||
G11 | Programmable data input cancel | ||
G12.1(G112) | Polar coordinate interpolation mode | Activate polar coordinate interpolation (G12.1) | |
G13.1(G113) | Polar coordinate interpolation cancel mode | ||
G17 | X Y plane selection | ||
G18 | Z X plane selection | ||
G19 | Y Z plane selection | ||
G20 | Input in inch | ||
G21 | Input in mm | ||
G20 | External radius / internal radius lathing and cutting cycle (G20) | ||
G21 | Threaded lathing and cutting cycle (G21) | ||
G21.2 | Threaded lathing and cutting mid-phase blade entry cycle (G21.2) | ||
G22 | Stored stroke check function on | ||
G23 | Stored stroke check function off | ||
G24 | Edge and surface lathing and cutting cycle (G24) | ||
G25 | Spindle speed fluctuation detection off | ||
G26 | Spindle speed fluctuation detection on | ||
G27 | Reference position return check | ||
G28 | Return to reference position | ||
G30 | 2nd, 3rd and 4th reference position return | ||
G31 | Skip function | ||
G32 | Thread cutting | ||
G33 | Thread cutting (G33) | ||
G34 | Variable—lead thread cutting | ||
G36 | Automatic tool compensation X | ||
G37 | Automatic tool compensation Z | ||
G40 | Tool nose radius compensation cancel | ||
G41 | Tool nose radius compensation left | ||
G42 | Tool nose radius compensation right | ||
G50 | Coordinate system setting/max. spindle speed setting | ||
G50.3 | Workpiece coordinate system preset | ||
G50.2(G250) | Polygonal turning cancel | ||
G51.2(G251) | Polygonal turning | ||
G52 | Local coordinate system setting | ||
G53 | Machine coordinate system setting | ||
G54 | Workpiece coordinate system 1 selection | Operating coordinate system configuration (G54~G59.9) | |
G55 | Workpiece coordinate system 2 selection | ||
G56 | Workpiece coordinate system 3 selection | ||
G57 | Workpiece coordinate system 4 selection | ||
G58 | Workpiece coordinate system 5 selection | ||
G59 | Workpiece coordinate system 6 selection | ||
G59.1 - G59.9 | 9 extra coordinate systems | ||
G65 | Macro calling | ||
G66 | Macro modal call | ||
G67 | Macro modal call cancel | ||
G68 | Mirror image for double turrets ON | ||
G68.2 | Tilted surface processing (G68.2) | ||
G69 | Mirror image for double turrets OFF | ||
G70 | Finishing cycle | ||
G71 | Stock removal in turning | ||
G72 | Stock removal in facing | Duplex cutting cycles (G72~G78) | |
G73 | Pattern repeating | ||
G74 | End face peck drilling | ||
G75 | Outer diameter/internal diameter drilling | ||
G76 | Multiple threading cycle | ||
G77 | Outer Diameter/Internal Diameter Drilling Cycle (G77) | ||
G78 | Multiple Thread Cutting Cycle (G78).. | ||
G80 | Canned cycle for drilling cancel | ||
G83 | Cycle for face drilling | ||
G84 | Cycle for face tapping | ||
G86 | Cycle for face boring | ||
G87 | Cycle for side drilling | ||
G88 | Cycle for side tapping | ||
G89 | Cycle for side boring | ||
G90 | Outer diameter/internal diameter cutting cycle | ||
G92 | Thread cutting cycle | ||
G92.1 | Default absolute zero coordinated system (G92.1) | ||
G93 | Inversed time feed (G93) | ||
G94 | Endface turning cycle | ||
G96 | Constant surface speed control | ||
G97 | Constant surface speed control cancel | ||
G98 | Per minute feed | ||
G99 | Per revolution feed | ||
G114.1 | Spindle synchronization function (G114.1) | ||
G114.3 | Spindle bearing function (G114.3) | ||
We defined that ANY machine operator should be able to use our Robotturn.
Our concept is meant to make turning more accessible, profitable and affordable.
CNC robotics, swiss type turning lathe, sliding headstock lathe, swiss lathe, screw lathe, swiss screw lathe, long parts lathe, high speed lathe, complex lathe, multi axis lathe, helvetian style lathe, cnc lathe