
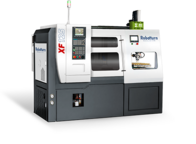
More info XF-Series
THE BASIC RELIABLE TURNING-CELL XF MODEL
Our new generation compact turning centers machines incorporate a wide range of enhancements that make Robotturn lathes better than ever. Our engineers reviewed and improved all aspects including motion control, integration of automation systems for material handling, coolant containment, chip evacuation, ergonomics, and serviceability – to create the highest quality, most reliable turning centers machine tools available. The XS Lathe range consists of a rigid flatbed structure made of high quality cast iron featuring high stability and good vibration dampening capacity.
• High Performance combined with SUPER compact design
• High flexibility: bar and chuck work
• Option for automation peripherals to meet any need.
The new design provides smooth chip disposal and easier operator access.
Robot handling
Shaft feeding
- parts diameter : Ø = 21/25 mm max
- parts length : L= 300 (800)mm max
- robot load 3kg x 2
- Payload 8kg
- Shaft loader :on demand
Pallet feeding
- parts diameter :Ø = 120 mm max
- parts length : L= 80mm max
- robot load 3kg x 2
- pallet diam 120 or 160 mm

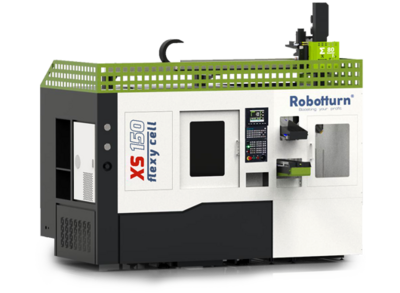
More info XS-Series
THE AFFORDABLE WORKHORSE : - XS MODEL
The XS Lathe range consists of a rigid slant-bed structure made of high quality cast iron featuring high stability and good vibration dampening capacity.
All the main casting components of the lathes are structural analysed by finite element methods (FEM). The boundary conditions are assigned reasonably and adequately to optimize the structures and rib distribution of the base, saddle and headstock to reach high rigidity and better stability.
The headstock is mounted on the same surface of the guide ways. This design shortens the transmission path of cutting force and stabilizes the cutting capability.
Major structural components have been combined into one solid platform. The low center of gravity 45˚ slantbed design provides the most rigid foundation possible for the headstock, turret, and tailstock.
Robot handling
Shaft feeding
- parts diameter :Ø = 40/45 mm max
- parts length : L= 330 (800)mm max
- robot load 5kg x 2
- Payload 12kg
- Shaft loader :on demand
Pallet feeding
- parts diameter :Ø = 160 mm max
- parts length : L= 100mm max
- robot load 5kg x 2
- pallet diam 160 or 200 mm

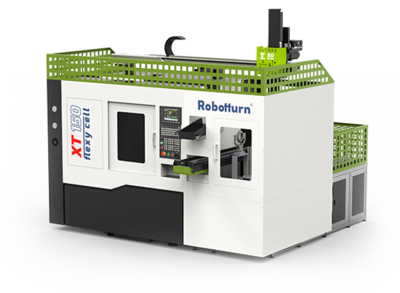
More info XT-Series
MAXIMUM STRENGTH & PERFORMANCE XT - MODEL
The XT range consists of a rigid single piece slant (inclined) bed structure made of high quality cast iron featuring high stability and good vibration dampening capacity.
The new XT range combines the slant bed with a hydraulic tailstock. Major structural components have been combined into one solid platform.
The XT series is capable of performing heavy-duty turning and maintaining long-term high-precisionaccuracy. More rigidity also means extended tool life. Built to withstand years of rigorous high production turning, the heavily ribbed, one-piece,thermally balanced bed and casting parts are of "Meehanite" casting.
The 45 degrees true slant bed design further provides superior support for the headstock, turret, and tailstock, thus, creating the rigidity neededfor long-term high precision turning and efficient chip removal.
Robot handling
Shaft feeding
- parts diameter :Ø = 45 mm max
- parts length : L= 370 (900)mm max
- robot load 8kg x 2
- Payload 15kg
- Shaft loader :on demand
Pallet feeding
- parts diameter :Ø = 200 mm max
- parts length : L= 150mm max
- robot load 8kg x 2
- pallet diam 200 mm
ALL the DIMESIONS OF THE CAPACITY OF THE GANTRY ROBOT ARE ONLY FOR STANDARD GANTRY GRIPPERS
BIGGER SIZE PARTS CAN BE HANDLED WITH OTHER GRIPPERS
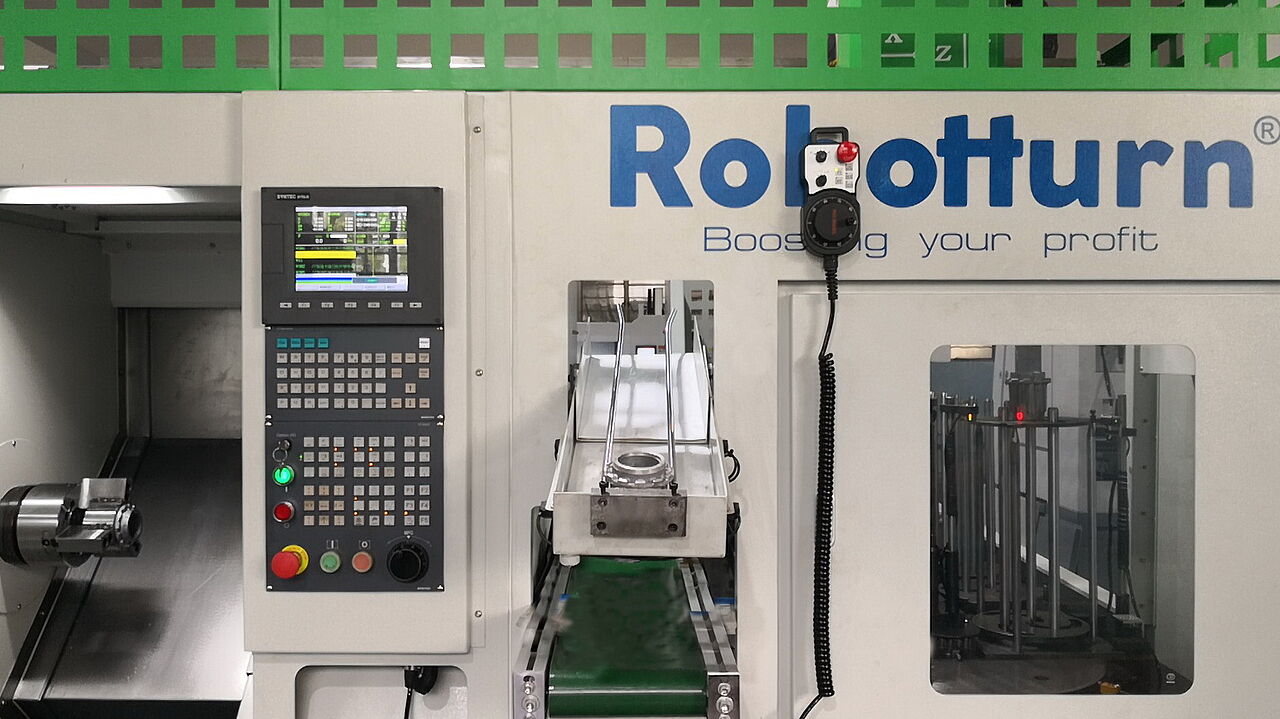
Robotturn - Boosting your profit
Our new generation of robot-lathes is on the way - smarter, more flexible, more adaptable and more affordable.
We bring major changes to the factory floor, as well to the global competitive landscape with our new Low-Cost Turning Cells.
Our latest models entering factories and being developed by our experienced engineering team are a different breed. They can work alongside standard CNC machines with the same operators and add huge productivity to your factory without any extra personnel needed. All are easy enough to program and deploy that you no longer need expert overseers.
That will change not only the way an increasing number of products are made. It could also mean an upheaval in the competition between companies. By reducing your labor costs, they also may allow yours and other high-wage countries to get back into some of the processes that have been ceded to China, central Asia, India, Africa, Mexico and other countries with vast armies of lower-paid workers.
Bar feeders, bar loaders, parts catchers, parts conveyors, overhead gantry loaders / unloaders, and integrated milling functions are all examples of turning center or CNC lathe automation. Each of these technologies serves to eliminate, reduce, or limit the amount of human intervention. Thus this improves spindle efficiency or increasing up-time, reducing operator error which reduces scrap while improving production rates and operator safety. Ultimately, this reduces cost/finish part.
There are a number of 3rd party suppliers for these technologies, but just like with all automation, that which is inherent to the design or built in by the machine tool OEM is the preferred choice.
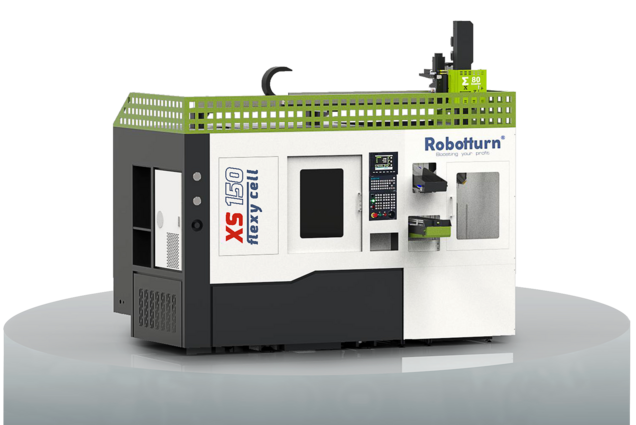
HIGH PRECISION ROBOTIZED CNC TURNING CENTERS
No compromise on quality!
Packed with industry leading technology and top-quality components, the Robotturn® X-series flexy cells combine power, strength, and speed to bring you the Ultimate Machining Power. These high speed machines will easily accomplish the demanding turning applications of today and tomorrow. Furthermore, with available live tooling and C-axis capabilities; milling, turning applications may be completed in one single machine.
The new design provides smooth chip disposal and easier operator access. Steel way covers and special steel wipers moulded with industrial strength rubber are used for durability. Fully enclosed splashguards keep chips and coolant contained for a safe clean working environment. The auto lubrication system delivers metered amounts of lubrication to the slide ways, ball screws, and vital components.
Why NOT adding a robot- cell to my existing lathe?
- Adding a robot to an existing lathe is not the optimal solution. Losing space in front of your lathe. Accessibility is reduced.
- Expensive: we offer a full cell where the others who offer only a robot for that price.
- With our solution we give you two running lathes with double output! Your existing one and a new Robotturn.
- Adding a robot to an existing lathe is increasing the capacity by adding some extra hours per day in production. We triple your capacity with a second robotized lathe and give you also all the benefits of a robot. One operator can run now more machines without any problem.
- With Robotturn : same investment, triple output, triple profit !
- Every operator from a cnc lathe can now handle easily extra one or more second robotized lathe.
- One controller for machine and robot : no interfacing problems and one supplier!
Basic Robotized Cell configuration
Robotturn FLEXYCELL- XS150+∑80
- Robotturn XS 150 with high speed super precision lineair toolholder
- recommanded: max parts diameter :Ø = 160 mm max parts length : L= 100mm
- Sigma 80 high speed gantry robot with load of 8 kg (2 x 4kg) max payload 10kg
- 8 palets APC diam 150 mm
- Dual robot-gripper
- Transport belt parts in/out for manual loading unloading
- Hydraulic 3 jaw chuck 150mm
- Chip conveyor to the back
- Parts Cleaning - drying Station operated by robot
- Quality control Chute with Zero defect logic for small series
- High speed 500/1000 blocks looking ahead controller
- HMI - Robot controller integrated in the CNC controller
- Optional active tool monitoring based on power
- Fully Ce protection around machine
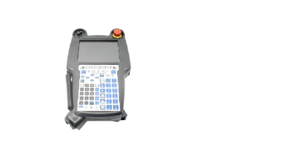
What does this button do?
Is this your operator's daily problem?
Is this not a question your machine operator is daily confronted with?
Perhaps you recognize the complex controller shown here?
Perhaps you find it scary to look at, let alone interact with?
It clearly radiates a complex and technical nature of interaction and understanding.
You most likely need extensive training to control that thing - right?
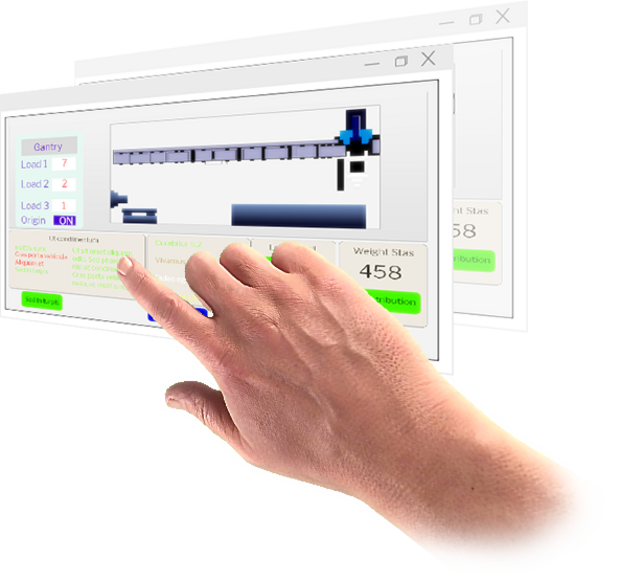
Time for a change
Robot graphic HMI - Human Machine Interface
We defined that any CNC operator should be able to use our Robotturn. Our concept is meant to make robotized turning cells more accessible and affordable. The complex pendant controller every robot maker is using is a huge bottleneck in that paradigm. The challenge consisted of redesigning the interface of the Robot. Rather than a pendant with hundreds of unknown buttons, that has been the standard since forever, we took a very innovative decision to use an interactive touchscreen with very simple graphic interaction, to control the robot-loader and kept the Lathe controller as standard. This means that the lathe can be used as standard CNC machine to make one single piece manually without interaction of the robot. All possible loading-unloading cycles are pre-programmed and the operator need only to fill in some of the values of the different stop/start points in the graphic interface. Simpler is not possible!
No robotics experience is required for the graphical robot controller. Our robot is already completely pre-programmed, so that the operator only needs to enter a few parameters. This means a new series can be started in a matter of minutes.
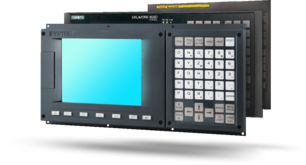
Only the best brands in CNC controllers
Get more for less!!
As a CNC controller is the heart of a production machine, reliability is the most important factor today. Robotturn® selected the 3 most reliable suppliers on the market today to serve our robotized turning cells. Fanuc and Siemens as the most sold controllers in the world and Syntec as the best value in the market, fully stuffed with all the thinkable options. Our Standard machines are equipped with the high speed Syntec TA controller with 500/1000 block ahead reading function, all turning cycles, high speed computing, graphical interface, mechatrolink® serial bus, etc. Syntec, based on long term OEM production for major Japanese CNC makers, offers a reliable high quality and a great value for money CNC package, including many more options than any other maker for which you must not pay extra.
Do you want to know all about our Robotturn ?
Call "Patrick" +32 (0)475736351 (Belgium)
He will explain you all about our Machines.
(Nederlands - Français - English - Deutsch)
Automated turning centers, automated CNC lathes, turning centers with automatic loading and unloading, turning centers with gantry loading and unloading, CNC lathes with automated gantry loading and unloading, robotic turning centers, robotic CNC lathes, turning center robotics, automatic CNC lathe part loading and unloading